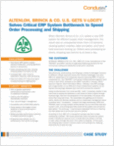 |
When ABC U.S. added a new ERP system for efficient supply chain management, the result was an unexpected strain from I/O demand, causing system crashes, data corruption, and handheld scanners locking up. Orders were processing so slowly, shipping was behind by at least a day.
Curt, Chief Information Officer, was able to run V-locity on several VMs, looking for improvements in workload processing. “We hadn’t even purchased V-locity yet, and we had full access to support. The ease of getting up and running was excellent,” he explains. “We tested the waters and, once I was confident nothing was blowing up, we pushed V-locity to the ERP hosts. I wanted to see the results in context of our biggest trouble spots before making a decision to purchase.”
Curt collected feedback from various business units, verifying V-locity’s impact. “Within days, I had reports back from shipping that scanners were no longer locking up, and there hadn’t been any system crashes,” he says.“That’s all the verification I needed.”
Since rolling out V-locity a year ago, there have been no system crashes, device lock-ups, and corrupted data tables. The IT resource dedicated to fighting fires is now doing the job she was hired for. “By getting rid of I/O, V-locity solved our problems, and I saved about $250K in hardware costs,” he explains. “Performance has improved so significantly, orders move from sales to shipping in real-time, saving a day of productivity. Now our biggest problem is we can hardly keep up with the pace of the orders. We’re more efficient than ever and people are back to loving their jobs.”
Read more by downloading case study!
Request Free! |